The major focus of most cylinder head discussion is flow into and out of the cylinder. While this is certainly an important function, consider that all the tuning efforts directed toward the induction and exhaust system is all aimed at getting air and fuel in or combustion residue out of the cylinder. Ultimately, all this effort is really focused on making cylinder pressure, which becomes torque and horsepower. Since the combustion process is what creates this cylinder pressure, it makes sense that we should pay particular attention to this process. What we’re talking about is the combustion space, which consists of the top of the piston and the cylinder head combustion chamber. It is the shape of this entire combustion space, including the top of the piston that helps shape the combustion process.
- Take the 100mm wide strips of galvanized sheet and cut them according to the required length of your brick - in my case 300mm - and add 10mm either end which you then bend at right angles to form an upstand to accept the dividing blocks. In the next step you nail these metal pieces along the length of the100mm wide plank as in fig.
- If you look at the inside of the caliper, you'll see a round piston. This is what pushes on the brake pads from the back. The problem is, the piston has adjusted itself to match your worn-out pads. Trying to get it over the new pads is like parking a Cadillac in New York City. You can do it, but the damage level will be high.
- Tip: Use Players from the same Leagues/Nations as the Brick Slots to get enough Chemistry.
This Tech Tip is From the Full Book, HIGH PERFORMANCE CHEVY SMALL-BLOCK CYLINDER HEADS. For a comprehensive guide on this entire subject you can visit this link:
LEARN MORE ABOUT THIS BOOK HERE
SHARE THIS ARTICLE: Please feel free to share this article on Facebook, in Forums, or with any Clubs you participate in. You can copy and paste this link to share: https://www.chevydiy.com/chevy-small-block-combustion-chamber-fundamentals/
Laying the Slot Block Laying the slotted blocks onto a normal depth mortar bed presses the mortar up into the multiple vertical slot cavities within the block, effectively increasing the surface area of the block in contact with the mortar.
In the early days of the smallblock Chevy and for all engines up to perhaps the mid-1970s, the shape of the combustion chamber was merely a tub or vessel in which to contain the valves. Little attention was given to the early small-block chambers other than the chamber volume’s affect on compression ratio. Generally, most performance small-block heads used a 64-cc combustion chamber roughly in the shape of a tub. The first major change to chambers came when emissions requirements led to increasing the size of the chamber to reduce compression and attempt to reduce the hydrocarbon count in the exhaust residue. This led to open chambers designed to reduce the quench area of the head, which also reduced oxides of nitrogen (NOx) emissions. This approach did not improve performance, however, especially given the accompanying drop in compression ratio.
This is an old 64-cc iron chamber from a 461 head—the classic “double hump” head that is still in favor with some small-block enthusiasts. While offering decent intake flow for its port size, this chamber does little to enhance combustion efficiency.
It’s difficult to measure how much a chamber is worth, but clearly this new generation of heart-shaped chambers is not as deep and tends to enhance mixture movement across the spark plug and toward the exhaust side. This is the new AFR 210 Eliminator chamber.
Into the ’80s and early ’90s, combustion chambers began to receive a bit more attention with an attempt to push or move the combustion process toward the exhaust side of the chamber. Heart or kidney-shaped chambers began to appear that not only improved flow out of the intake valve, but also attempted to encourage mixture movement toward the exhaust side of the chamber. Angled spark plugs also began to appear with some regularity accompanied by information that suggested that the spark plug could improve combustion by beginning the event from a more advantageous position.
This is an old 64-cc iron chamber from a 461 head—the classic “double hump” head that is still in favor with some small-block enthusiasts. While offering decent intake flow for its port size, this chamber does little to enhance combustion efficiency.
This is a factory LS7 chamber for the GEN IV 505-hp small-block used in the 2006 CZO6 Corvette. Note how the chamber wall is laid away from the valve to mirror the flatter valve angle and the long side radius to improve port flow.
The tighter the radius between the intake valve and the chamber wall on the short or back side of the chamber the less flow that will result. A gentler, smoother radius improves flow and creates more even air-fuel distribution around the entire valve circumference.
Several cylinder companies offer CNC-machined chambers as an option. If the price is right, these precise chamber mods can make more power. This is the new AFR 180 Eliminator chamber. Note the very fine lines created by the CNC machining.
It’s only been since the 1990s that serious OEM work has begun on attempting to improve power by evaluating the combustion event using in-cylinder pressure analysis and more accurate dyno testing to evaluate what really occurs in the cylinder during combustion. A big revelation was that the shape of the combustion chamber does have an immediate and worthwhile affect on combustion efficiency. This is one reason why late-model GEN III and GEN IV engines are capable of running 11:1 static compression ratios with relatively short intake duration numbers on 91-octane fuel and still survive a 100,000-mile durability test. These engines also enjoy the benefit of electronic spark control that pulls timing out of the engine as soon as detonation is detected, but there are still many things that we can learn from these combinations.
Combustion chamber shape is actually dictated by several conditions. First is the valve angle, which for a production-based GEN I smallblock Chevy is 23 degrees. As we saw in Chapter 9, a shallower angle is beneficial from a flow standpoint, and this also creates a shallower combustion chamber, which aids in creating compression. The standard small-block 23-degree angle dictates a somewhat deeper chamber. You may have also heard of angle-milling heads. This “roll-over” technique changes the deck angle relative to the valves, but at best this is worth only a degree or so. The main reason for angle-milling heads is to remove more material from the deep side of the chamber in order to reduce chamber volume to increase compression. The chamber must also accommodate the valve sizes. With the small-block now capable of 454 ci or more of displacement with talldeck versions, valve sizes have had to grow as well—well surpassing the 2.02/1.60-inch standard. In fact, it’s possible now to get as big as a 2.250- inch intake valve for larger smallblock race heads.
Squeezing in the spark plug location is another critical component of combustion chamber design. Ideally, the spark plug should be in the geometric center of the combustion chamber where the flame front is required to travel the shortest distance in any direction to complete combustion. With a 4-valve per cylinder chamber or a Hemi, this is very easy to achieve. With a wedge-type chamber, the valves occupy this real estate, requiring the designer to move the spark plug over to the exhaust side of the chamber. In the 1970s, one of the first racers to discover that an angled spark plug was worth a little power was the late Smokey Yunick. Angling the spark plug toward the exhaust valve not only places the plug closer to the center of the cylinder, but also directs more of the combustion process toward the exhaust side of the chamber. Most newer aftermarket heads also use long-reach plugs not only to increase thread engagement in aluminum heads, but also use this longer reach to place the business end of the spark plug closer to the center of the cylinder.
According to Darin Morgan, the engine specialist at Reher-Morrison Racing Engines, the slight depression in the face of most intake and exhaust valves can create small vortices that are capable of disrupting the combustion process. This may be the case with tight chamber volumes in Pro Stock engines, but probably not worth the effort in a street engine. The recesses in the valves are there to reduce valve weight.
The back radius of an intake valve is an area that gets little attention. Always use 12-degree back angle valves. The 10-degree valves are lighter, but offer a flatter angle that doesn’t flow as well. On the exhaust side, sometimes a tulip-style valve can enhance flow, but you should flow test this before using these valves.
There is some evidence to show that a radius on the face of the exhaust valve offers some exhaust flow improvements. This becomes a situation where individual exhaust ports or applications will dictate its use. Don’t be afraid to try this to see if it works.
Jim McFarland championed the use of strategically placed dimples in combustion chambers and on piston tops as small vortex-generators. The theory is that these dimples tend to create more chamber activity before combustion starts.
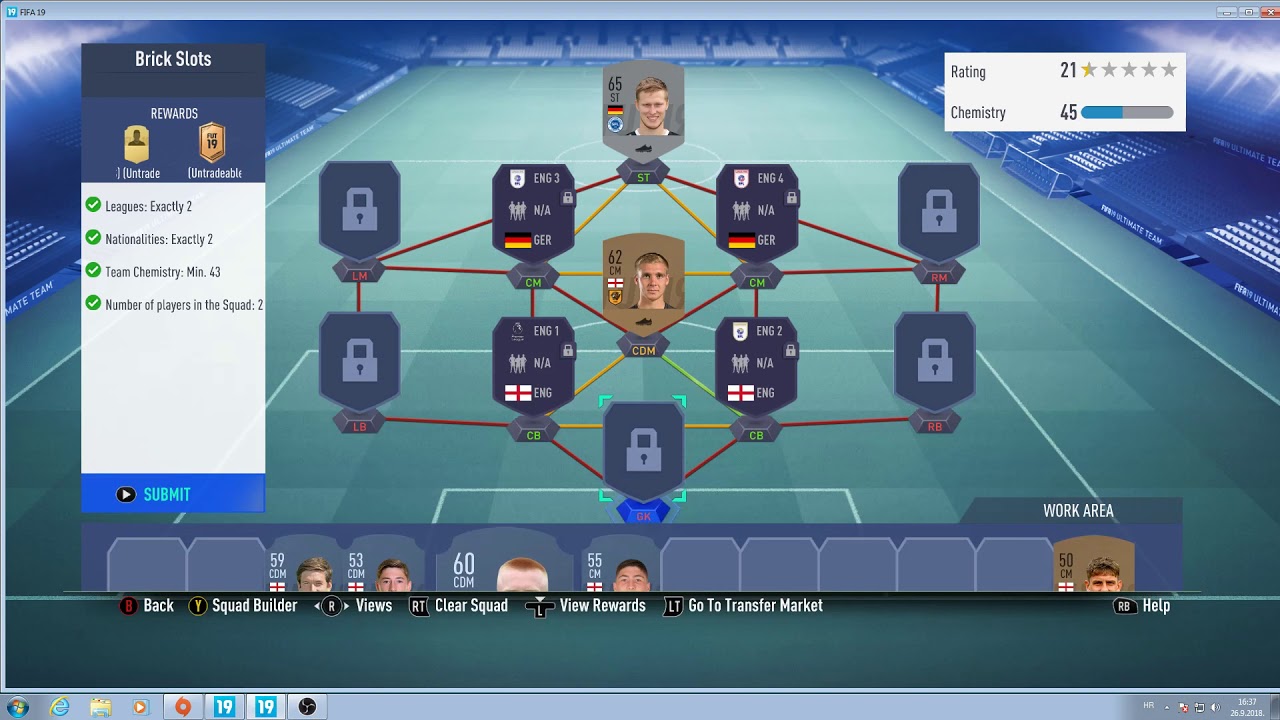
Chamber Shape and Wet Flow
While it may seem that the chamber shape is dictated by some mystical attempt to direct the combustion event, most cylinder head designers will tell you that the chamber design is actually dictated by the ports. Let’s take a look at what occurs here, which should give you a better understanding of combustion chamber design and their functional requirements. As mentioned earlier, early chambers were mere deep tubs. As the chambers became shallower, this unshrouded the valves, improving flow. Taking this one step further is the concept of thinking of the chamber wall that continues the long side radius of the port as a continuation of the valve angle. As we mentioned in Chapter 9, with flatter valve angles, this becomes even more relevant. Laying the chamber wall back in an attempt to continue the flow out of the valve only improves flow. This is why even slight chamber modifications on production heads can improve flow even after the air has moved past the intake valve into the chamber. If the chamber wall does not pinch off or impede flow coming out of the valve, airflow generally improves at all valve lifts, but especially at the higher valve lifts.
Chamber shape is also critical as it relates to the wet flow aspects of chamber dynamics. Most of the discussions about intake ports and chamber shape tend to be concerned only with the effect of changes on dry airflow because that’s been the predominate method of testing until now. But with the advent of wet flow testing, the effect of the intake port and chamber design on the wet flow aspects can no longer be ignored. Chamber shape and the exit of the air and fuel out of the port and into the cylinder have a big impact on power and efficiency. We’ve included photos of this effect from Dart’s wet flow bench on how the liquid fuel enters the cylinder. Currently this evaluation, by design, does not take into account the effect of the piston moving up or down in the cylinder, but these rudimentary first steps still reveal a startling picture of what happens to the fuel as it enters the cylinder.
We’ve stated in this book that high-end racers and cylinder head developers often acknowledge and have experienced multiple examples of where their dry flow test bench has “lied” to them. Some use their flow bench only occasionally to help in development. In talking with the guys at Dart, and specifically to cylinder head specialist Tony McAfee, it’s very possible that changes to the port that contribute to dry airflow improvements actually make the dynamic wet flow picture worse. Then, when the cylinder heads are actually tested on the engine, the results are disappointing, or as one wag put it: “We’re suffering from improvement, again.” The Dart guys were less than forthcoming in terms of specifics as to where or how this happens, perhaps because we were knocking on a door they have just recently opened themselves. Clearly, this is an area that offers tremendous opportunities that are only now beginning to be explored.
Reading combustion chambers in an effort to evaluate combustion activity and efficiency is an art form that is elusive at best. Fuel wash creates clean areas, as does complete combustion efficiency. Fuel wash is evident with most cylinder heads near the intake valve where liquid fuel tends to keep that portion of the chamber clean. Look for an even grayish-brown residue as an indication of good combustion activity. Greasy, black smudges generally indicate rich air-fuel ratio concentrations that slow the combustion process.
This photo reveals very poor combustion activity on the piston top where we have both clean areas as well as rather greasy and inconsistent results of combustion. This engine would not respond to tuning and was down on power mainly due to an improper match of pistons and combustion chamber.
There are other cylinder head designers and port specialists who are still professionally skeptical and prefer to design their ports based only on what they see on the dry flow bench along with the results they see on the dyno. While the wet flow controversy will continue to flourish in the coming years, so will evidence that proves to be either a colossal waste of effort, time, and resources, or the next new frontier in which numerous revelations in newfound power will emerge.
It’s essential to always match the correct spark plug with the right cylinder head. Most aluminum heads use 3/4-inch long-reach threaded plugs to engage more threads in the softer metal. Iron heads use the shorter-reach plugs. The long-reach plugs use a gasket for sealing while the short-reach plugs generally use a tapered seat.
Extended tip spark plugs are great for everyday driving, but with higher engine speeds, more compression, and/or higher cylinder temperatures like with nitrous you better be using a short nose plug. The shorter tip uses a shorter ground strap path to the head. A longer ground strap can act like a glow plug if it overheats. This can cause serious pre-ignition damage.
Clues to Combustion
We have included some photos of combustion chambers that have been colored by use and there is a time-honored tradition of attempting to evaluate combustion efficiency by “reading” the tracks in the snow, if you will, left over from the combustion process. This usually takes extensive experience and more than a little bit of art combined with a small amount of science. The first and easiest areas to identify are the clean portions of the chamber. Generally, these appear most frequently adjacent to the intake valve against the steep chamber wall. This is most often the result of fuel wash, where liquid or semi-liquid fuel merely washes clean any combustion residue. One attendant theory about clean areas of a chamber (or areas with the lightest deposits) is that this is where combustion efficiency is highest. There is certainly evidence to support this, often found in the simplest of places. If you look closely into a wood-burning fireplace, notice that the bricks nearest the flame tend to be clean and without residue, while farther away from the hottest pat of the flame, black combustion residue begins to form on the brick surfaces. The theory here is that the intense heat of the combustion process burns away the carbon while father away from the flame, this carbon has a chance to deposit.
Dart’s Platinum iron heads have relocated the spark plug deeper into the chamber and closer to the exhaust valve in an attempt to improve combustion activity. The closer the plug is to the geometric center of the combustion space, the quicker and more complete the combustion process.
The same kind of evaluation can be made in the combustion chamber. What we’re looking for is a chamber with an even pattern of combustion across the entire chamber: with an even coating on the piston top, chamber floor, and walls as we get closer to the exhaust valve area of the chamber. Ideally, the combustion space will be evenly colored, but in reality that rarely occurs. Each cylinder exhibits its only special “footprint” that, if evaluated closely, can offer clues as to the combustion space’s efficiency. Large areas of fuel wash are not good, neither are centralized areas of heavy, sooty-black carbon deposits. These are signs of poor combustion activity where the flame front either fails to travel or offers very little heat to eliminate the carbon deposits. Small, clean spots along one side of the spark plug boss are also commonplace, but this also indicates fuel movement across the spark plug. A well thought-out chamber will attempt to push the fuel in a circular motion exiting the intake port, moving the air/fuel mixture across the spark plug and toward the exhaust side of the chamber.

Angled spark plugs have been around for a long time. Few enthusiasts know that the idea is to move the plug closer to the exhaust side to help push the combustion process to that side of the chamber. This outstanding example is the fully CNC-machined LS7 combustion chamber.
It’s also common to see the exhaust valve a slightly lighter color than the rest of the combustion chamber. This can be attributed to the exhaust valve’s higher operation temperature. An exhaust valve with carbon deposits is clearly not running at its peak temperature, which indicates the cylinder is not running anywhere near its peak potential. All of this information can also be used to help evaluate the piston top as well since it constitutes the “floor” of the combustion space. Because the small-block is a wedge engine, the quench area is generally clean since little combustion occurs in that area, but the rest of the piston should reveal evidence of equal heat if the chamber space is efficient.
We have included a couple photos of a small-block dyno test where the cylinder head modifications were not positive, resulting in an engine that did not respond well to changes (oftentimes not responding at all), while also requiring more ignition timing and much more fuel than a comparable engine package where the combustion space was far more efficient. Once we removed the cylinder heads, the residual burn patterns on the top of each piston clearly indicated that the engine was not performing the combustion process efficiently. There were large clean spaces on the pistons tops where there was no combustion activity present, matched by a center area of the piston evidenced with irregularly shaped areas of greasy black, sooty combustion residue. It was obvious very quickly that this engine was just not happy and the chamber modifications we had tried did not work.
Along with all the other spark plug data, colder plugs are essential for a high-RPM street engine to keep the engine out of trouble. Colder plugs transfer more heat away from the plug so it doesn’t overheat. On long, high-speed runs the plug can overheat and turn into a glow plug that can take out pistons, ring lands, and even whole engines if the problem is severe enough.
Combustion chamber and piston coatings are becoming more popular and more durable. They do offer protection from damage during lean mixture runs or heat damage from a too-hot spark plug. Dart now has an in-house coatings department that can coat chambers or valves right from the factory.
One advantage to aluminum heads is it is easy to repair or modify ports, or in this case the combustion chamber. Here, aluminum weld has been added to repair a combustion chamber. This puts a bunch of heat into the chamber, which will require heattreating the head and all new seats and guides.
The point of this is that during disassembly, there are many clues to how well the engine is running, far beyond just the power numbers displayed on the dyno curve. So the next time you tear that small-block apart, take some time to look at what the piston tops and combustion chambers are telling you. It may even be worth it to take some digital photos that you can later evaluate on your computer in more detail.
Conclusion
There are few areas in the internal combustion engine that are more shrouded in mystery, yet offer the most potential for gain than the combustion space. We are learning more every day about not only how air and fuel enter the cylinder, but also what happens to that mixture after it has been oxidized and the clues that the combustion process leaves behind. It’s up to the detail-oriented hot rodder and engine builder to decipher these hieroglyphics using a little bit of common sense and a keen eye for the smallest of combustion clues. It’s fun. You ought to try it.
How To Do Brick Slots Sbc Fifa 20
Written by Chris Petris and Posted with Permission of CarTechBooks
How To Do Brick Slots Sbc Play
GET A DEAL ON THIS BOOK!
If you liked this article you will LOVE the full book. Click the button below and we will send you an exclusive deal on this book.